Det er tidlig på nittitallet. Bedriften på Lunde, der hundrevis av søgninger, songdøler og andre har hatt sitt daglige virke og innkomme gjennom årene, er meldt konkurs. Driften hos Brødrene Repstads Karosserifabrikk A/S har stoppet opp.
Av Håkon Repstad sr
NB: Intervjuet med Torje Egeli ble gjennomført høsten 2021, noen uker før Egeli gikk bort.
Der et tusentalls nye busser er produsert og hvor det hvert år rullet ut omkring hundre nye, som deretter gikk i rute over det ganske land. En hjørnestensbedrift, hvor fellesskapet dannet bidrag til kommunekassa og den gangs velferd.
Noe står igjen
Bygningsmassen i betong står igjen. Mengder av produksjonsteknisk utstyr og materialer for bussproduksjon ligger ubrukt. Bedriften på andre siden av Føssa, vis-a-vis den gangs Søgne og Greipstad Sparebank, er gått inn i historien. Åtti år med teknologi under utvikling. En omtale av kvalitet og ordentlighet, som strander før ny-teknologiens fremtid blir tilgjengelig, slik andre bussprodusenter også opplevde det på denne tiden. Hva nå?
Historie
I Kristiansand er to flinke arbeidskolleger ansatt ved Grubernes Sprængstoffabriker A/S. Det er på sekstitallet og selskapet beslutter i 1971 å fusjonere med konkurrenten, Norsk Sprængstofindustri A/S. Den nye organisasjonens navn blir så til Dyno Industrier A/S. Med det er norsk sprengstoffproduksjon samlet i en organisasjon og de ansatte i Grubernes i Kristiansand tilhører fra nå av Dyno Industrier A/S. Rasjonalisering og effektivisering ligger bak.
Torje Egeli og Per Gyberg
Det var på dette tidspunktet to arbeidskamerater, Torje Egeli og Per Gyberg, evnet å omsette innovative tanker til praktisk handling. Torje Egeli var formann hos Grubernes. Han hadde erfaring og interesse for det tekniske i bedriften, mens kollega Per Gyberg hadde spesialkunnskap og erfaring med vakumforming av plastmaterialer. Arbeidskameratene bestemte seg så for å starte egen bedrift med plastproduksjon på Utkjerr i Songdalen. Med på laget var også fabrikksjef Kjell Karlsen. En nedlagt to-etasjers kolonialbutikk, ble til Gyli Plast A/S.
Plassen på trehundre kvadratmeter ble fort for liten og kravet til ventilasjon i produksjonen var av stor betydning. Innetemperaturen kunne bli høy, og det ble vanskelig å drifte forsvarlig etter de retningslinjene myndighetene krevde.
Artikkelen fortsetter under bildet.
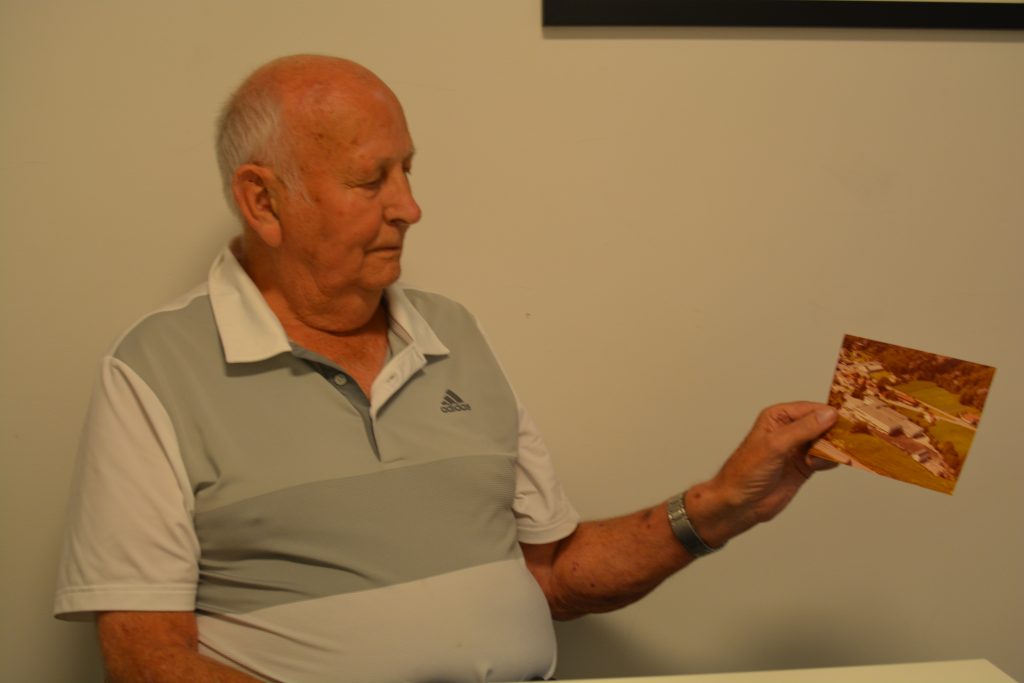
Torje Egeli (84). Foto: Håkon Repstad sr.
Krevde nye tiltak
Arbeidsmiljø og fremtidens produksjonsvekst krevde nye tiltak, og det endte opp med nytt bygg på Spjotneset, i samme kommune. Nå en bygning på ellevehundre kvadratmeter, og man tenkte at man kunne bli der inn i fremtiden. Men igjen meldte behovet seg for større plass, og det ble midlertidig løst ved å leie tusen kvadratmeter i nabolokalene tilhørende Agdermaskin A/S. Bedriften vokste seg stor og sterk og det ble arbeidsplassen for mange.
Jeg har avtalt å møte tidligere leder Torje Egeli (84). Vi setter oss på biblioteket på Tangvall hvor han med ærbødighet forteller meg litt av sin historie fra yrkeslivet.
– Per og jeg forstår etter hvert at enda en utvidelse må til. Geografiske sonderinger og tilfeldigheter gjør at lokalene til Brødrene Repstad på Lunde i Søgne blir ledige. Etter noe om og men byr vi på konkursboet og tilslaget kommer. Fem millioner måtte til. Vi fikk det rimelig. Alt hadde gått fort. Samtidig spilte kommunen på lag med oss og alle de tretti ansatte ble med på flyttelasset til sitt nye arbeidssted, Lunde i Søgne.
Mangt måtte håndteres og avvendes
I kjølvannet lå avviklingen av karosserifabrikken, samtidig med vår innflytningsprosess. Over hundre garderobeskap kom for salg, maskinpark, materialer, mye plast og profiler i aluminium likeså. Mangt måtte håndteres og avvendes. Utstyr ut og nye maskiner og utstyr inn. Mye kostbart i aluminium beregnet for bussproduksjon. Materialer til et nytt spennende busskonsept likeså, men som ikke kunne nyttiggjøres. Det måtte pakkes og sendes tilbake til leverandøren i Sveits.
Etter innflytning var vi i gang med produksjonen etter ei ukes tid. Folkene våre sto på. De kom til bedre forhold, og fikk nytt bonussystem som gjorde at de tjente bra. De ønsket seg til og med spisesalen lokalisert midt i produksjonshallen, for dermed å kunne ta spisepausen uten å måtte stenge ned produksjonen. Da fikk de full kontroll med mye av den automatiserte driften. Ansatte viste lojalitet og innsats, og bonusen lå selvsagt og fristet. Det var gøy å få det til. Men vi jobbet helst litt for mye. Det jeg ikke hadde sett for meg skulle skje, var at min kollega Per ble syk like etter innflytning. Det skapte selvsagt vanskeligheter for oss, og det skulle ta lang tid før han igjen kunne komme tilbake.
Storproduksjon
Produktene bedriften produserte var i stor målestokk ventiler og ventilsystemer til oljeindustrien, også til den finske traktorprodusenten, Valmet. Det var betydelige leveranser i termoplast. Til kjøleindustrien var det innredning til skap og disker. Lampetter bør nevnes. Den populære Disney lampen, barneværelselampen som vi lagde hundretusener av. Helheten bidro til solid drift med en positiv bunnlinje i regnskapet.
Produktene våre er et resultat av forming. Først lages formen i tre før den så overføres til en sand-støp for derfra å bli formet i materialet sluttproduktet skal representere. I kjøleprosessen av denne støpe-teknikken er millimeternøyaktigheten krevende. Materialet kryper ved nedkjøling, derfor er det vanskelig å beregne det nøyaktig sluttproduktets målstørrelse. Det trengs med andre ord erfaring og fagfolk.
Ble forespurt om storleveranse til Volvo
Torje Egeli forteller videre. – Bedriften ble ved en anledning forespurt om storleveranse til Volvo personbiler. Regnestykket og vurderingen endte opp med et – nei! I telefonsamtalens løp måtte vi avslå tilbudet. Vi måtte rett og slett si at vi ikke var interessert. Det gikk et par dager så fikk vi igjen telefon fra Sverige. Om det var mulig å komme å besøke bedriften vår? Representanter fra Volvo ønsket å se den bedriften i Norge som takket nei til store bestillinger og mulig fremtidig samarbeid med svensk bilindustri. Jeg forklarte grunnen til avslaget, fortsetter Egeli. – Nå er vi omkring 40 ansatte i produksjonen. Slik vi forstår det vil selv en liten del av de ønskede produktene være ensbetydende med ansettelse av ytterligere 40-50 medarbeidere for å holde unna. Så i løpet av noen få år vil nye bilmodeller kreve at vi igjen må konkurrere med andre produsenter i markedet. Taper vi da så sitter vi igjen med en mengde ansatte for mye. Delegasjonen fra Volvo skjønte dette. Vi hadde ikke interesse av å ekspandere. Vi tjente bra, var fornøyd og hadde mange storhets år, men jobbet helst litt for mye.
Kostnadsbevisstheten var dårlig
Selv om driften var bra, var kostnadsbevisstheten også viktig. Flere store elektriske porter inn til bedriften var kostbare å drifte i forhold til års-sertifisering. Dermed reduserte vi til to porter som igjen reduserte driftsutgiftene. Også lederne måtte ta et tak i produksjonen til tider. Egeli forteller om et fin-besøk fra utlandet, hvor vedkommende direktør nektet å håndhilse på han. – Jeg hadde litt plastspon på hendene og gikk i kjeledress.
Vår nærmeste støtte i bedriften var hele tiden fabrikksjef Kjell Karlsen. Han hadde vært vår daglig leder og disponent den gang vi jobbet for Grubernes – som ble fusjonert til Dyno Industrier A/S. Etter fusjonen ønsket Kjell heller å bli med oss til Gyli Plast A/S. Han var enormt flink, en dyktig medarbeider og språkkyndig.
Et retningsvalg måtte tas
Torje Egeli fortsetter. – Min kollega Per, kom så etter hvert tilbake til bedriften etter langt sykefravær og fremtiden krevde retningsvalg. Alle årene vi hadde hatt sammen var gode og utviklende. Veivalgene hadde vi enes om, men ønskene for fremtiden måtte vi igjen klarlegge. Det utviklet seg ulike målsettinger og positiv uenighet om det beste for fremtiden for Gyli Plast A/S. Også dens behov for kun en leder. Vi forstod begge at over tid ville bedriften tjene på det. Det var da etter noen tid det ble naturlig for meg å selge aksjepostene mine til Per. Mange flotte år sammen, men retningsvalget måtte gjennomføres. Det var økonomisk riktig for alle parter å løse det slik vi gjorde. Sammen dannet vi grunnlaget for fremtiden og fremtiden er i dag. Gyli Plast A/S fremstår utviklet med dagens modernitet og teknikk. En flott og viktig industribedrift på Lunde i Søgne, som har sin årelange historie hvor jeg i sin tid var delaktig. –Tenk om en hadde vært tjue år på nytt, sier Torje Egeli, med et smil, vel vitende om at bedriften han en gang hadde vært med å starte, nå har utviklet seg til å bli en av Norges største og blant Skandinavias ledende produsenter innen vakuumforming av termoplaster.
Fakta:
Bedriften Brødrene Repstads Karosserifabrikk A/S var virksom fram til 1990, da gikk den konkurs. I løpet av årene 1925 og fram til 1990 skal den ha produsert ca. 5000 busser. BRK var i mange år den største arbeidsplassen i Søgne og på det meste var det 100 ansatte. Området der den første bedriften lå, går fremdeles under navnet «Smietomta». De tidligere fabrikklokalene etter karosserifabrikken er i dag eid av Gyli Plast A/S, en av Norges største og blant Skandinavias ledende produsenter innen vakuumforming av termoplaster.
Brødrene Repstads Karosserifabrikk A/S – siden Gyli Plast A/S. Foto: Skappel og Størmer.