Hver mandag, tirsdag og fredag kjører fullastede trailere med varer fra Gyli Plast AS på Lunde i Søgne til et internasjonalt marked med ditto kundeportefølje. Et marked med mange konkurrenter og med budrunder som i forkant av produksjonen kan være tøffe. Vi er her sammen med lagersjef Svein Gyberg. Han forteller om dagens produksjon, om markedet og litt om opprinnelsen til bedriften.
Av Håkon Repstad
– Aksjeselskapet tilhører familien Gyberg. Broren min, Per, døde for et par år siden. Gyberg-navnet stammer fra Hægebostad. Per og hans tidligere arbeidskamerat, Torje Egeli, var opphavsmenn til bedriften, som i sin tid startet på Utkjerr i Songdalen. (I nummer ni 2021 av Fritidsnytt står beskrevet mye av historien frem til 1990 tallet.)
Har vært i produksjonen siden 1972
Vi er tre interesserte i følget, Tore Hodne, Frithjof Bay Gundersen og undertegnede, som har fått lov til å besøke bedriften. En times ekskursjon, ledet av lagersjefen, som umiddelbart inngir tillit.
Han har vært i produksjonen siden 1972 og kjenner rutinene og produktene ut og inn. En kompleks produksjonslinje bestående av store tekniske maskiner i kombinasjon med moderne elektronikk, som igjen overvåkes av dyktige operatører med variert opplæringsbehov.
Vi forstår ganske snart at Svein Gyberg er en person som ivrer etter å formidle oss og omverdenen hva bedriften står for, både med hensyn til kompetanse og hva den betyr i markedet. Samtidig en bedrift som de fleste ikke kjenner så mye til, men som har vært arbeidsplassen for mange. En bedrift som også ønsker å ivareta yngre interesserte som skal oppleve en god start på yrkeslivet.
Artikkelen fortsetter under bildet.
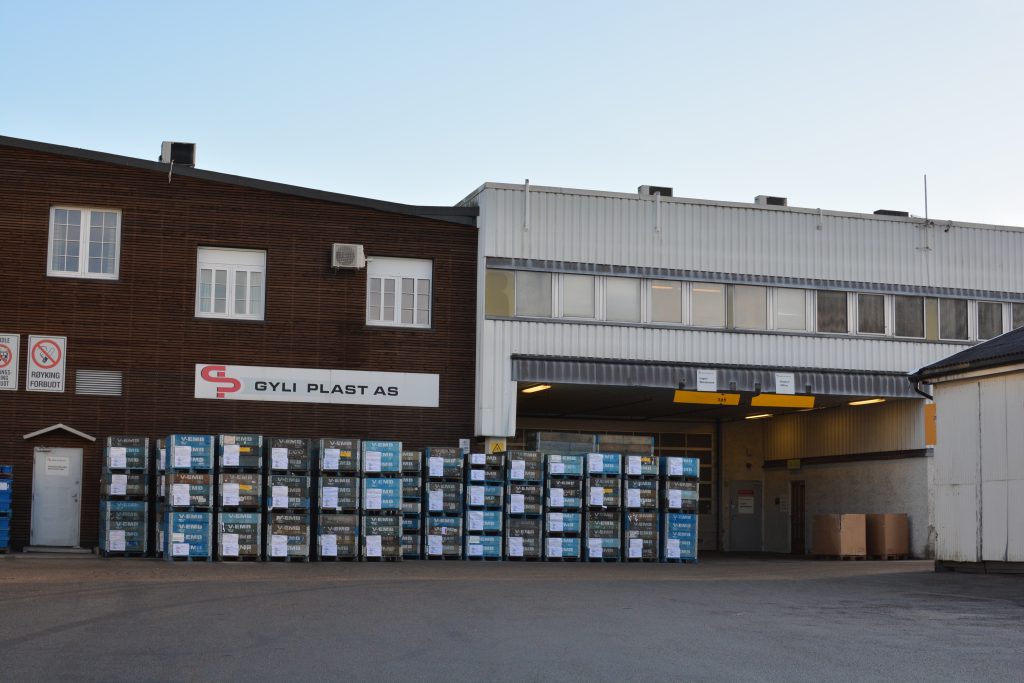
I flere tiår har Gyli Plast på Lunde levert sine produkter world wide.
Nøyaktighet, kvalitet og lojalitet
– Nøyaktighet med leveranser, kvalitet i produktene og lojale ansatte har vært altomfattende viktig for at vi er der vi er i dag. Svein Gyberg peker på en tilfeldig trekasse, fylt med plastprodukter, med adresse Mexico. – Ti tusen kroner betaler vi i frakt for denne. Med bil og båt tar transporten tretti dager. Skulle vi sendt kassen med fly, ville frakten blitt det tredobbelte. Planlegging og punktlighet er alfa og omega. Kundene må kunne stole hundre prosent på oss. Filosofien her er å få produksjonen unna så fort som mulig.
I den innledende delen av ekskursjonen samles vi i spisesalen. Vi serveres kaffe og kommer i samtale om koronasituasjonen som er og har vært. Tjueseks av omkring førti ansatte ble syke, mens avtalene for leveranse måtte stå som avtalt. Med denne erfaringen er vi besøkende plassert i god avstand til hverandre.
50 år i 2023
– Lydnivået er tidvis høyt i produksjonshallen, så jeg anbefaler dere å benytte hørselvern. Neste år er bedriften vår femti år. Fra starten på Utkjerr, til nye lokaler på Nodeland og så hit som vi er i dag. Marnardal ble også vurdert, men jeg er glad valget ble hit, selv om vi igjen nå opplever å vokse oss noe ut av nåværende lokaler. Noe av grunnen er behovet for stor lagerplass. En del voluminøse plastprodukter, som for eksempel skibokser, tar plass. Vi ønsker i den grad det er mulig å sette bort monteringen av disse til eksterne underleverandører. Nevnes kan Vennesla-bedriften A3 ressurs, som driver med arbeidstrening.
Desidert størst i landet
På spørsmål om bedriften har konkurranse i Norge, forklarer Gyberg at Gyli Plast AS er den desidert største i landet.
– Vi er en nisjebedrift, men har mange konkurrenter i Sverige, samtidig som Sverige er et godt marked for oss, på grunn av Volvo. Dertil et høyt volum. Vi er til sammen tre vakum-formings-bedrifter som leverer til Volvo. To i Sverige og oss. Så hver gang det er snakk om et nytt produkt blir anbudsrunden spennende. Spørsmålet vi stiller oss er om vi fortsatt klarer å bli med videre.
– Innredning til store hjullastere og gravemaskiner er produkter vi leverer, mens vi fortsatt takker nei for leveranse til personbilproduksjonen. Borerigger, tilhørende Atlas Copco, som brukes av Nye Veier AS, er vårt marked. Også postbilene som bygges i Fredrikstad innredes med våre produkter.
Fire til åtte tusen enheter i året
– Vår produksjonsform er forholdsvis sen, vi anslår mellom fire til åtte tusen enheter i året. Da er også jobben vår regningsvarende. Til personbilproduksjonen er man fort oppe i tjue tusen enheter i året. Den baseres på en helt annen produksjonsform, såkalt sprøytestøpning av granulat, mens all vår produksjon er fra plater i plastmateriale.
Gyberg forteller om da han begynte i sommerjobb i 1974.
– Egentlig har jeg vært med helt fra begynnelsen av. Jeg har ingen eierforhold i selskapet annet enn at jeg har jobbet for min bror i alle disse årene. I sin tid gikk jeg på Agder Distriktshøyskole, kjemilinjen. Siden var det meningen å reise til Bergen og studere marinbiologi, men slik ble det ikke, og valget ble å være trofast for min bror i bedriften.
– Jeg startet som produksjonsoperatør, ble videre produksjonssjef og fikk siden spørsmål om å gå inn i salgsapparatet. Etter hvert ble det til at jeg overtok ansvaret for lageret, noe jeg siden har ledet. Jeg trives med å være i bevegelse.
Egen verktøymaskin
– Per i dag har vi en hovedansvarlig tekniker hos oss, likedan en tegner. En egen verktøymaskin brukes til å lage former av aluminium, vårt verktøy for bruk ved vakumforming. Alt fra deksler i forskjellige størrelser og form. Mange av dem varianter til bruk offshore. Til det kreves et materiale som er selvslukkende, i tilfelle brann.
– Et krav til materialet med en såkalt brom membran. Vi kjøper inn de spesifikke materialfargene kunden måtte ønske. Plata formes etter den på forhånd maskinerte aluminiumsmodellen.
– Vakumforming ligger i navnet. Ei plate som oppvarmes, som igjen omslutter forma ved hjelp av undertrykk. Av formene har vi utallige modeller liggende som vi altså produserer selv.
Har også produkter i hardplast
Gyberg viser frem et spesielt glasshardt produkt, bearbeidet av polykarbonat. En hardplast som benyttes i en rekke plastprodukter, som visst nok ble oppfunnet i 1952 ved en tilfeldighet. En kjemiker blandet forskjellige oljer og parafiner. En reaksjon skjedde og materialet ble unnfanget.
Videre nevner han fordelen med plaststøtfanger, der man kan rette ei lita bulk med varmt vann som helles over. Et typisk produkt er dette lanterneglasset. Gyberg holder det i handa fremfor oss.
– Disse benyttes i livredningsbåtene som slippes ut i fritt fall. Glasset lages i poliskjold carbon, et uknuselig produkt av samme kvalitet som politiet benytter i sine hjelmvisir. Lanterneglassene koster omkring sekshundre kroner per stykk. Materialet er kostbart og lages i forholdsvis små volum. Det tar sin tid å forberede prosessen, maskinene må rigges.
Taxilamper
Så viser han oss et nytt produkt, taxilampa, den velkjente taklykta. Så en beskyttelsesskjerm som terrenggående rullestoler benytter. Deretter dekslet som benyttes i hytta på de store Volvo-maskinene.
– Her er et høytalerlokk. Skal jeg tippe har vi et titalls tusen forskjellige artikler som er bygd på ditto former av aluminium. Ved bestilling tilsendes vi datafiler, freser så ut forma, som altså danner grunnlaget for produktproduksjonen. Her er deler av ei førstehjelpsdukke, laget i abs-plast. Disse sender vi til USA. En modell med hudfarge og en med karbon-mønstret overflate.
Artikkelen fortsetter under bildet.
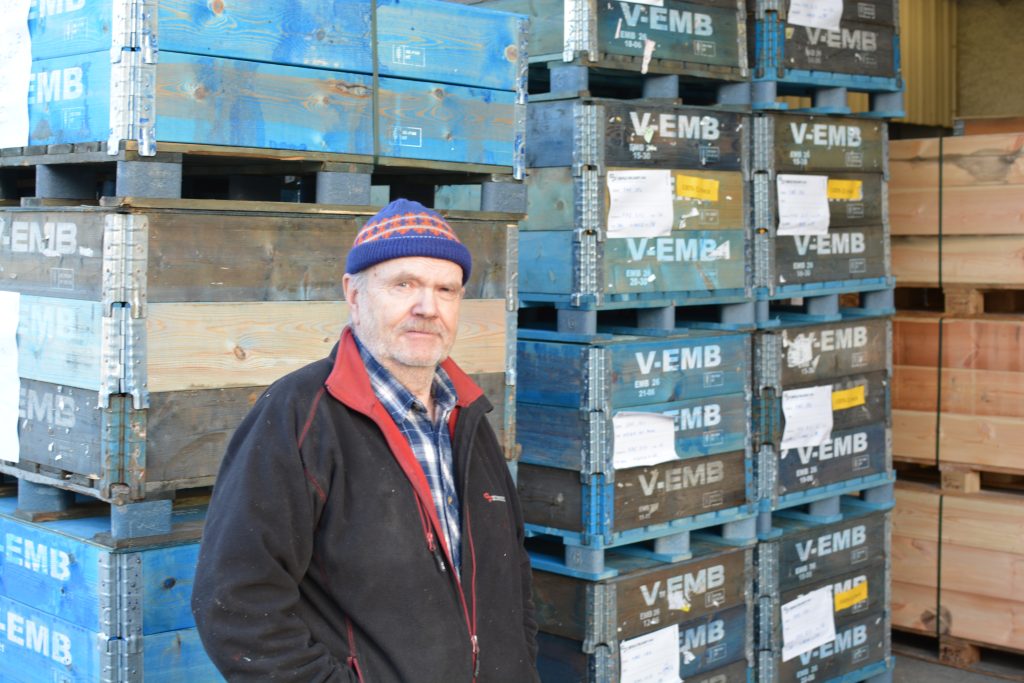
– Nye produkter er pakket og gjort klare for utskipning, sier Svein Gyberg.
Forsendelse til Mexico
– Disse blir videre forberedt med plass for diverse følere og forskjellige detektorer. Nylig hadde vi en forsendelse til Mexico. Ganske sprøtt, sendt fra lille Gyli Plast AS i Søgne. Platematerialene vi benytter kommer vesentlig fra Sverige og Irland. Vi shopper der det faller rimeligst. Da pandemien kom ble det kjempeproblematisk å få tak i pleksiglass. Alle skulle ha dette til beskyttelse i butikker og andre servicetjenester. Vi måtte støvsuge markedet. Vi skårer høyt på leveringspresisjon. 99,8 prosent er ganske heftig.
På spørsmål om hvem som er så glupe å få til slike salg?
– Ja, si det, svarer Gyberg.
– Vi har flinke folk på salg. Eksempelvis er vi i Sverige fast en sammenhengende uke hver måned. Oppsøkende og kontaktskapende virksomhet, i tillegg til et godt rykte med kvalitet i produktet, bidrar dette til fremskrittene vi trenger.
Leverer til en lang rekke land
– Vi leverer produkter til Brasil, USA, Belgia, Bulgaria, Portugal, Mexico og Sverige. Som nevnt tre trailere i uken. Årsomsetningen vår ligger på omkring 70 millioner, mens lokalitetene best tåler en årsomsetning på 50 millioner. Vi er altså litt på «overtid» med hensyn til plassbehov. Det begynner å bli trangt. Vi må kanskje igjen ut og leie mer lagerplass, på samme måte som på Spjotneset i Greipstad i sin tid.
På spørsmål om det er mange ekskursjoner ved bedriften, så forteller han om periodiske besøk fra UIA, gjerne kunstfagstudenter, elever som vil forsøke seg litt med arbeid på plastprodukter og samtidig få litt kjennskap til produksjonsformen.
Flere vakumformingsmaskiner
For å forstå produksjonsformen ved vakumforming kommer han inn på dette spesifikt. Vi står i nærheten av en av fire store vakumformingsmaskiner fra Italia. Enkelt forklart blir aluminiumsforma tilhørende ønsket sluttprodukt satt ned i maskinen.
En materialplate av formingsplast mates automatisk inn over formen og varmes opp til omkring 170 grader. Varmeelementene trekker seg så automatisk tilbake og aluminiumsformen føres opp mot og inn i den oppvarmede platen. Så suges all luft bort, det blir undertrykk i området, og platen suger seg inntil og omkring formingsmodellen og danner formen aluminiummodellen innehar.
Blir formstabil
Det finner sted en tosidig oppvarming av materialplata. Etter formingsprosessen kjøles platematerialet ned til omkring 70 grader og er med det blitt formstabil. Deretter følger bearbeiding og klipp av platematerialet, som nå har blitt til et grovprodukt i prosessen.
– Vi kverner selv overskuddsmateriale til granulat og sender det videre i sekker til Sverige. Det er gull for oss. Nytt råstoff koster førti kroner kiloen, mens kvernet materiale kjøper vi tilbake for ti kroner kiloen. Hadde vi ikke hatt den muligheten hadde vi heller ikke eksistert. Prisene er presset og det er om å gjøre å benytte seg av detaljene. Det blir altså en viktig faktor i bedriftsøkonomien og dermed bedriftens bunnlinje. Vi ligger på et dekningsbidrag på mellom 3% til 5%, så volumsalg er viktig for oss. Hvilken bakgrunn har så de som jobber her? Det er lite opplæring som skal til for å kunne betjene maskinene. Vi har egne programoperatører.
Gyberg forteller om produksjon av skiboksene. Bunnen leveres fra Tyskland. Twin-sheet forming. To plater i bunnen blir formet sammen til en bunn. Disse boksene er store og tar mye plass. Vi ønsker slik sett å få satt bort monteringen av disse på grunn av plassbehovet.
Lagersjefens time har gått fort. Vi har lært en masse om en bedrifts innhold ikke så mange kjenner så mye til. Vi takker for omvisningen og overrekker Svein Gyberg en liten blomsterbukett, som et lite bidrag. Som svar: – Har dere fått utbytte av besøket er min dag reddet. Akkurat slik som dette har jeg ønsket så mange ganger. En åpen dag, hvor publikum kan komme her å se litt av produksjonen vår, få en kaffeskvett og noen nystekte vafler – så fantastisk det hadde vært å presentere oss for nærmiljøet.